Weatherizing an Old House: An MLK Day Service Project
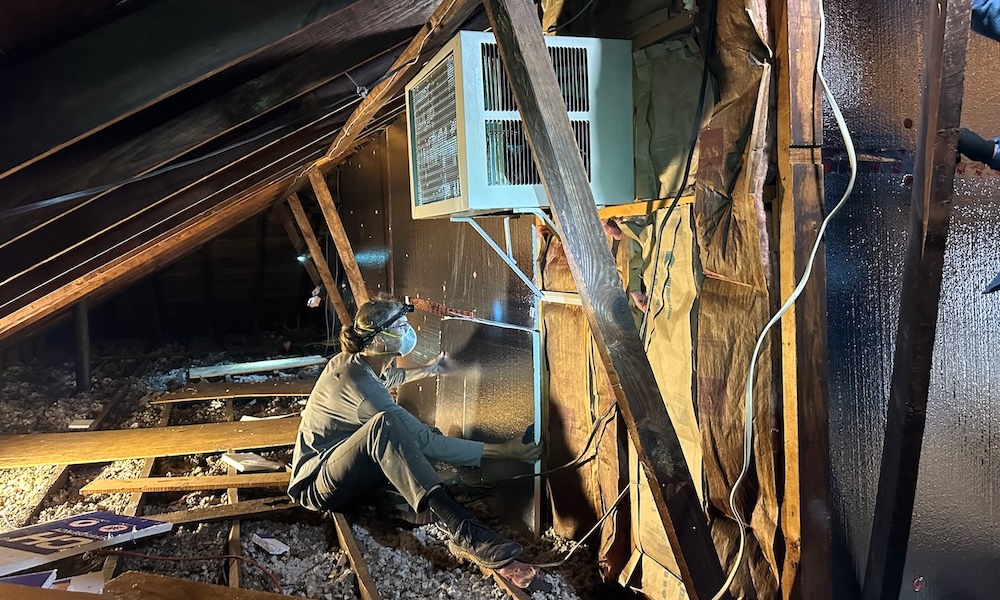
A lot of volunteers gathered in Decatur, Georgia this past weekend for the annual Martin Luther King Jr. Service Project. They worked at a number of sites doing all kinds things to improve the homes of low-income senior citizens. The jobs volunteers worked on included cleaning out homes, replacing broken stuff, installing handicap ramps, general maintenance, and more. I participated this year and was on a crew led by Mike Barcik, a friend and former colleague from days working at Southface. Our job was weatherizing an old house. Here’s how it went.
A huge hole beneath the sofa
If you’re doing a volunteer project to weatherize an old home in three days, you want to look for the low-hanging fruit. That is, find the stuff that will make the biggest difference with the least amount of work and that volunteers can be shown how to do without much difficulty. The house I helped with had one huge piece of low-hanging fruit that Barcik is pointing to here.
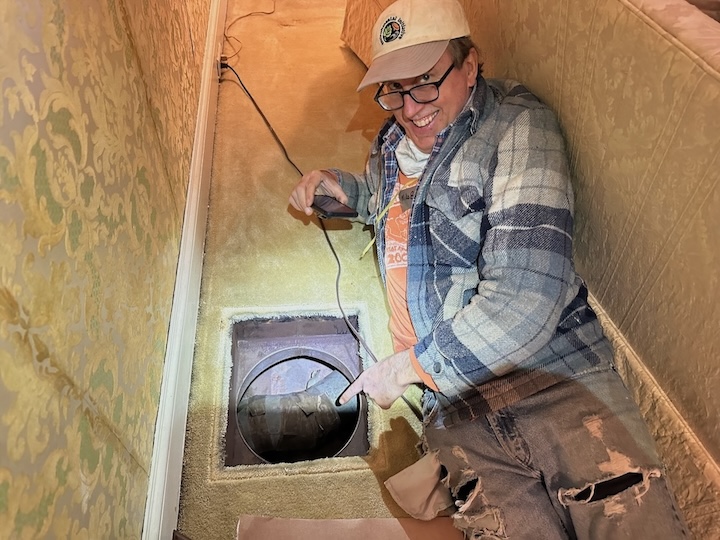
Someone pulled the sofa away from the wall in the living room and exposed a huge hole in the air barrier. It looked like an ordinary return vent in the floor, but when they removed the grille they found there was no duct attached. That 12 inch diameter hole was wide open to the vented crawl space below. That meant that drafts, moisture, and critters had easy access to the living space.
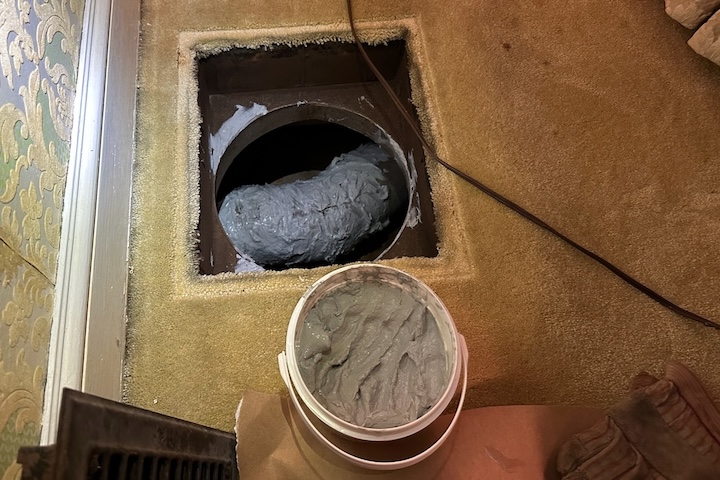
The fix began with using mastic to encapsulate the tape on the duct below. That kind of tape on old ducts almost certainly contains asbestos, so this is a good way to keep the fibers out of the air. Then they put three layers of foam board into the hole, sealing around them with spray foam. Then the grille went back over the now sealed hole.
Typical attic kneewalls
In weatherization world, any wall that separates unconditioned attic from conditioned space is called an attic kneewall. They’re notorious sources of comfort and energy efficiency problems. Why? Here are the main reasons:
- Lots of air leakage sites
- Fiberglass batt insulation installed poorly
- Open floor joists that allow hot or cold attic air to get under the conditioned space floor
I’ve written about kneewalls several times in this space (see related articles below) and also spent quite a bit of time fixing them back in my contracting days.
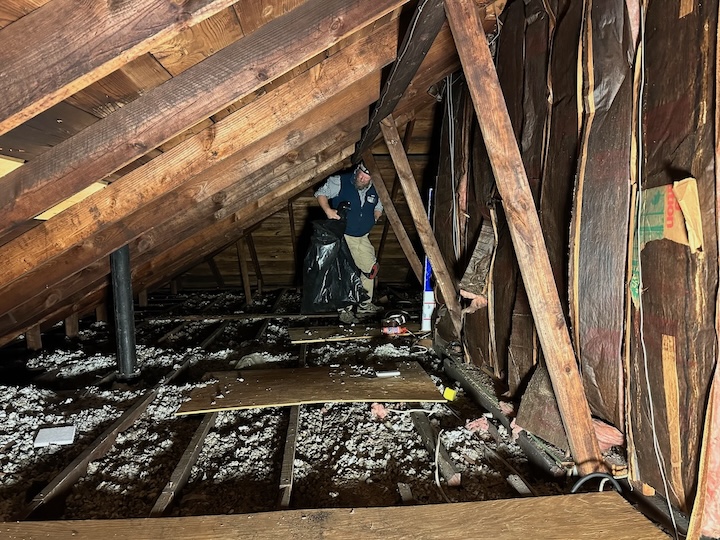
The attic kneewalls in this house had the typical problems. You can tell that room on the other side of the kneewall had problems because there’s a window unit air conditioner in the kneewall. The photo above shows Energy Vanguard’s Jeffrey Sauls getting ready to fix one of the kneewalls before we did anything to it. The lead photo at the top shows Chris Thiele working on that same kneewall.
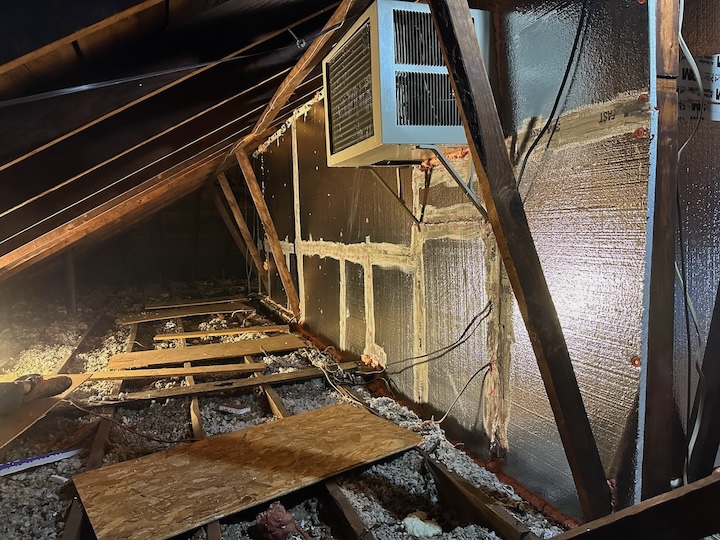
And the photo above shows what that same wall looked like at the end of the long weekend project. The fiberglass batts are now covered with rigid foam insulation, and the seams are sealed with tape and mastic.
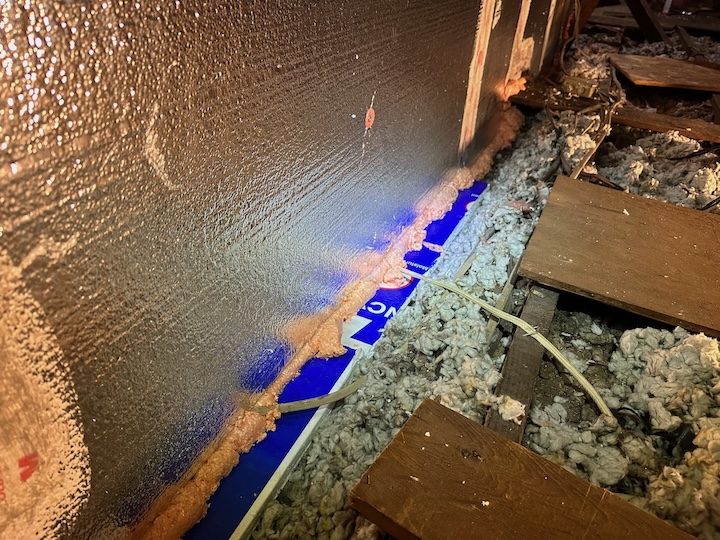
It’s important to fix the whole kneewall, though. The photo above shows the foam board and spray foam sealing everything up at the bottom. The devil, as always, is in the details.
A wiring warning
When weatherizing an old house, it’s important to understand the risks that come with the territory. In this house, the risk that threw up a roadblock was the old knob-and-tube wiring in the attic. This is a hundred year old house, and that’s what they had in the 1920s.
So what does this mean? The Building Performance Institute (BPI) has standards and certifications for energy auditors and says this in their technical standard for envelope professionals:
Insulation may not be installed where live knob and tube wiring exists.
The problem is that the cloth insulation isn’t durable and can expose live wiring. That could lead to electrical shocks or fires.
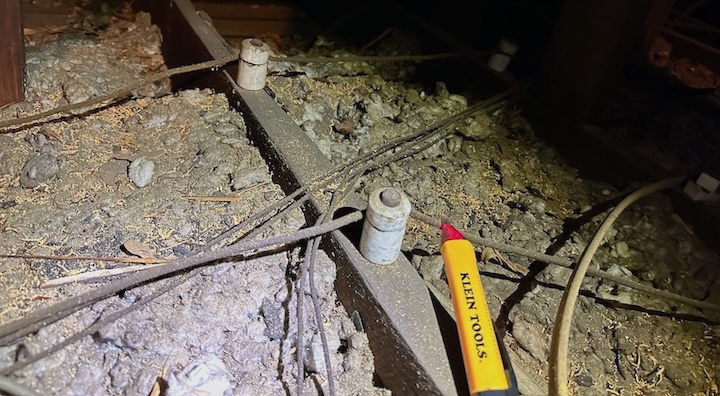
So we tested. The photo above shows the tester lighting up red, indicating that the wire is still energized. So were all the others we found. That meant that we couldn’t add insulation to the attic floor until the knob-and-tube wiring all gets replaced.
Working at the eaves
Even though we couldn’t insulate the attic over the weekend, we did get it ready for insulation. The prep work consisted of doing two things at the eaves. First, the house had balloon framing in the exterior walls, which means the walls were open at the top.
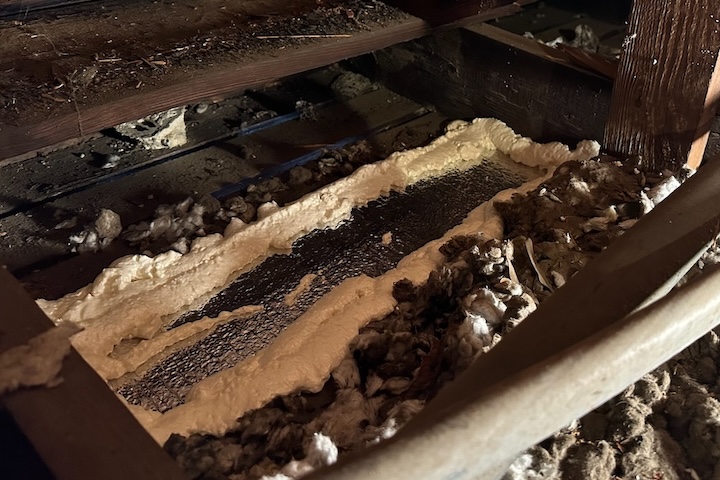
In the photo above, you can see a piece of foam board sealed into place at the top of one of those uncovered wall cavities.
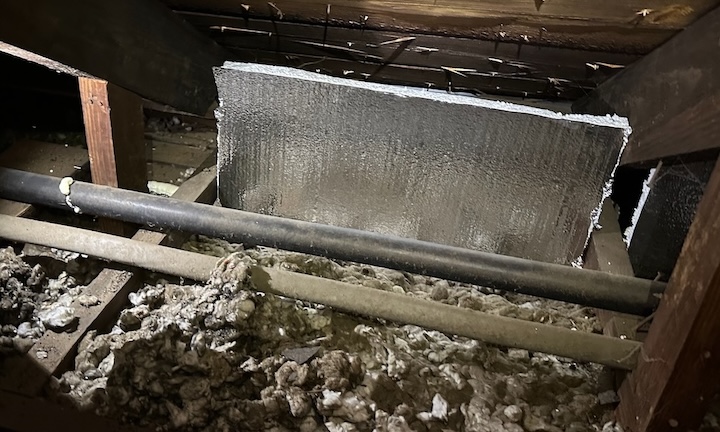
The other prep job was to put insulation dams in place to keep wind from blowing through the insulation and degrading its effectiveness, as you see in the photo above.
One improvement in the basement/crawl space
I spent my working time in the attic, but volunteers also did a little work in the basement/crawl space. They insulated the water pipes. With the weather that’s has come in since the weekend—a low of 14 °F (-10 °C) this morning—that probably made a difference for them.
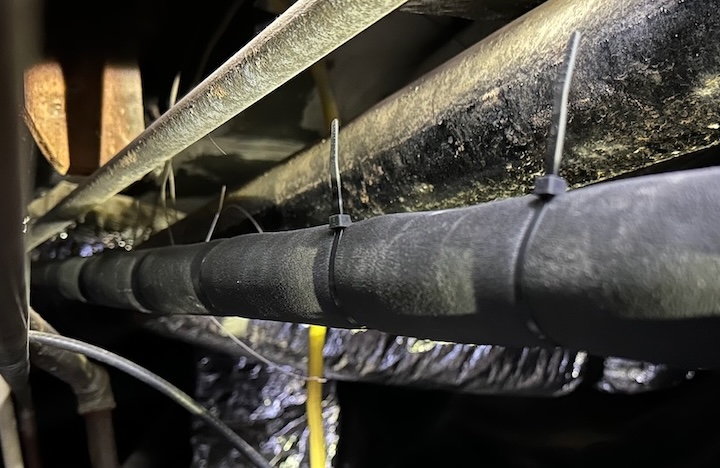
Giving back to the community
I was one of many people who worked during the MLK Service Project over the holiday weekend. This article in Decaturish has a lot of photos showing some of the things that people worked on.
I think we made a significant difference in weatherizing an old house for that family in Decatur. The reduced air leakage and improved kneewalls should help with comfort and energy efficiency. If you’re in the Atlanta/Decatur area, consider donating or signing up for next year. If you’re not local, look for similar projects in your area. If there aren’t any…hey, you can start one!
Allison A. Bailes III, PhD is a speaker, writer, building science consultant, and the founder of Energy Vanguard in Decatur, Georgia. He has a doctorate in physics and is the author of a bestselling book on building science. He also writes the Energy Vanguard Blog. For more updates, you can subscribe to Energy Vanguard’s weekly newsletter and follow him on LinkedIn.
Related Articles
How to Sheathe an Attic Kneewall — And How Not to
Hidden Air Leakage Sites in Your Attic
Comments are welcome and moderated. Your comment will appear below after approval.
Thanks to Allison and Jeffrey of Energy Vanguard for your help along with a number of other current and former Southfacers and many other community volunteers at this and other houses. I’m guessing well over 1,000 people participated in this amazing MLK service project!
I’m happy to say that we sealed that 1 foot diameter hole first with roll flashing and sheet metal screws (to deter critters) and then layered in foam board that was sealed with mastic. It’s always great to enact a big fix like that right before the cold weather hit this week.
Gratitude all around, -mike barcik
Mike: The real thanks go to you and Frank for all the work you’ve done with this project for more than 20 years now! And thanks for providing the details about how you sealed that hole.
This really was news from the front! That is a very cool project, Allison. Will you folks be making it out to blow in some new insulation once the knob and tube is taken care of? It’s always amazed me how much of that stuff is still around.
How did you find the hole under the couch? Did you think to look or was there an obvious draft?
Scott: The plan for the weekend was to fill the the joist cavities and then insulate with rolls of fiberglass insulation over the top of the joists. That may not happen till next year now. I’m not sure how they found the hole under the couch, but my guess is they were looking for vents they could seal with mastic from the inside. Maybe Mike will provide the answer.
Allison,
What a great project! I’m sure the fixes kept this house from a few broken water pipes and cozier days and nights in this frigid weather.
Yes, it is, Loretta!
A great service and will have to participate with this next year. Any other Organizations to recommend in the Atlanta area for 2024? Post had lots of good starting points to help with older homes, thank you Allison!
Eric: This is the only one I know about for this type of project, but there may be others.
I inspected over 3,000 houses in my 10-year Home Inspection career and saw quite a few attics like that in SE Ala., but I never saw a window unit from that viewpoint. My 1890 family homeplace is in need of many improvements energy-wise, beginning with the establishment of the thermal barrier. I appreciate you sharing your knowledge and especially this particular project. Houses of that era present special challenges of which many experienced and qualified people are ignorant. That’s okay. We are all ignorant, except on different subjects. Thanks Will Rogers.
Syd: Yeah, that window unit in the kneewall is a sure sign they had heat gain problems in the summer.
Nice work Allison !
Someday I’ll have you guys redesign the duct work in my townhome. I’m just waiting for a lightning strike to burn it to the ground or one of the large Oaks to fall on it. 😉
Interesting stuff in those attics… Knee walls are kind of a new thing here in TX as 2 story houses weren’t very common place until the last 10 years or so. I would personally never own a two story house unless the kitchen, master BR, living room were on the main level.
Before christmas I spent a day insulating the attic some more. I wasn’t able to get out to the edges and install any good baffles because the pitch of the roof so when you blow it in you just bounce it off the decking and keep as much in the attic as possible. Ended up putting in 46 bags and I wasn’t able to move the next two days. Low pitch roofs suck. I had planned to do it last spring but we went from winter to 110* like flipping a light switch.
I will say that over the last few days when it was 10* for around 10hours straight and not much warmer during the day the heater ran noticeably less than I expected. Basically just a little more than it would have on a typical cold winter day. The real test will come when the miserable season starts called summer. Oh and the garage never got below freezing since I also insulated it at the same time.
Once I’m done remodeling the house I’d like to encapsulate the crawlspace but it’s hard to find good companies to do that here since crawlspace houses are a rarity and only in houses from the early 60s and older. I’m too old to crawl around there and do it anymore. Hopefully we will move to a cooler state before I need to have it done…
Our standard practice has been to get a short list from the head of the MLK Service project. The candidates are usually houses that have had some form of other repair done in prior years – plumbing, structure, ramps, painting, etc. – they are “in the system”.
We pick a few houses to inspect and try to gauge ease and appropriateness – we generally select 2 homes plus a 3rd in case we finish early. Sometimes we do pre-blower door testing but our time up front is often limited. Later, we can do test out – I have some data where we’ve easily obtained at least a 25% reduction and some as high as 70%!
Our standard effort is to pull registers, wash them, shop vacuum as far in as we can reach, and then seal the duct from the inside with mastic and the boot to the subfloor (and then replace the register). We correct or at least clean out the dryer vent as well. We often seal AHU and plenum connections too (if they are accessible). All of this is fairly volunteer friendly.
My wife actually led the effort of the duct upgrades and showed me the giant hole – I glanced down and thought it was a duct running through a bigger duct. We felt cold air and quickly realized it was a hole to the basement dirt floor.
With more volunteers, we might have gotten more done below the house but this project focused heavily on the attic and knocking out around 500 s.f. of kneewalls was a major effort. Once they rewire and remove the old knob and tube, we’ll see about completing the rest of the attic – more balloon frame blocking, soffit dams, raised and insulated catwalks and storage platforms, and adding more loose-fill insulation.
While this is the first time I’ve encountered a window unit in a kneewall (BTW, we did airseal it from the inside), it’s not the first time we’ve had a register with no boot that connects directly to the foundation! Crazy stuff is more common than you think! Cheers, -mikeb
Allison: Awesome job in support of those in need!
Question which comes to mind – when you were adding the rigid foam to the kneewall, did you take any steps to prevent cold (or hot, in summer) air from running under the interior floor?
Tom: Yes, on the two sides where the joists were open to the area beneath the floor, we sealed them with foam board and spray foam.
Does it matter if you use XPS or foilfaced Polyiso foam board?
How did you attach the foamboard? Roofing nails with wide heads?
What type of tape did you use to seal the edges of the foamboard?
Thanks!